Surface Flaws
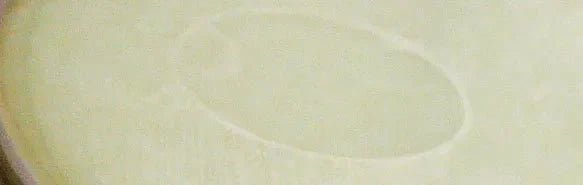
Surface Flaws
Surface flaws can result from a number of different issues. The most common cause is devitrification. This is a change in the chemical structure of the glass from being amorphous to crystalline, causing the surface to lose the glossy appearance that is characteristic of glass.
How do I avoid devitrification?
Devitrification or devit shows as a scummy white haze on the surface of glass after firing. It is usually caused by contamination such as finger prints, sticker residue, grinding marks and dust. To avoid devit, clean the glass using glass cleaner and paper towel, protect the glass from dust before firing and use our basic full fuse firing schedules. If you still get devit after following these steps, try firing onto shelf primer rather than thinfire (this is essential if you have been grinding the glass).
If devitrification does occur, you can use clear powder to remove it. Take a look at this tip sheet for more information: How to Fix Surface Flaws.
I used 3mm fibre paper as a shelf separator. It left a rough white surface after firing which does not come off even after brushing under running water. Why?
3mm Fibre is not suitable as a separator for fusing as it will stick to glass in certain circumstances. Fibre is used instead of a shelf by some people and when used in slumping will release, it can also be used in casting to form a barrier; generally opal glass will stick to fibre more than transparent glass. The specific preparations for separating glass from the shelf are Thinfire Paper and Bullseye shelf primer.
How do I prevent my cast piece from having sharp edges? If it does get sharp edges how can I remove them?
Sharp edges occur on cast pieces when the glass scrapes down the sides of a casting mould during firing. To prevent this make sure that glass is positioned in the mould so that it flows out to meet the edges of the mould, rather than scraping down the sides of the mould and getting caught.
Sharp edges can be removed using various cold-working methods, ranging from using simple hand tools to using dedicated cold-working machines. We offer a range of tools suitable for all kinds of cold-work. See our hand tools and our range of cold-working machines.
How can I prevent suckers?
Suckers are unsightly depressions or wrinkles that can appear when casting. They are caused by differences in temperature during the cooling process, as thinner areas will cool more quickly than the rest of the piece.
To prevent suckers, keep your glass at a uniform temperature during cooling by soaking/holding the glass at 677°C to thoroughly unify the temperature, then cooling gradually to the annealing phase.
How can I prevent band saw cuts from causing devitrification on 3mm thick glass?
If you grind glass prior to firing, it can cause the cut edge to devitrify on firing. This can be reduced by keeping the piece wet when grinding and cleaning the cut with a toothbrush under a running tap, this gets all the loose bits out of the cut. Then fire the piece onto shelf primer rather than thinfire as the smoke from the thinfire can help to kick off devitrification. If you fire at 333C per hour between 677C and 804C this will also help.
When firing to a full fuse, my shelf primer adhered to the glass. I needed to use a diamond hand pad to remove it. What went wrong?
Shelf primer usually only sticks if it has been fired before, it is too thick, or if the primer is very old. Outside of this, primer can stick when the firing is too high. Take a look at our Kiln Schedules page for tried and tested schedules for use with Bullseye glass. If none of these factors are the case, you can only resolve the issue by using Thinfire paper rather than shelf primer.