Stress & Cracks
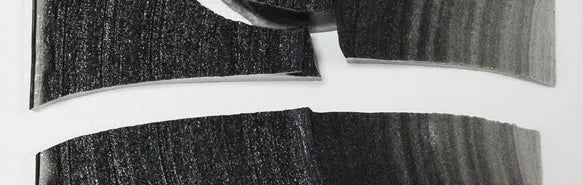
Stress & Cracks
Cracks are usually the result of stress in the glass. Stress can be caused by a number of factors, like heating the glass too fast or not annealing correctly.
Why has my glass cracked during firing?
There are three reasons for glass cracking in the kiln:
Incompatible glass – This will only happen if you use glass from different manufacturers and is identified by the crack running around a piece of glass in the design.
Thermal shock – This is due to heating too fast or cooling too fast. Soft edges in the break indicates heating too fast and sharp edges on the break indicates cooling too fast.
Poor Annealing – Annealing should be calculated according to thickness (about 1hr for 6mm). If your design has different thicknesses the annealing hold should be doubled
For our recommended firing schedules, see our Kiln Schedules page.
My casting has cracked, can I fix it?
Some cracks are fixable and some are not. It depends on the crack, how severe it is and where it is on the piece. If the crack is very large or on the interior of the piece, the only thing you can really do is recast the piece, as no repair will make the crack disappear sufficiently. This is the same for thermal shock, as the edges of the crack will have rounded off, and also if your piece has stuck to the mould making material. In all of these cases, before recasting you should review your casting method and make improvements to stop the piece cracking again. If the crack is not on the interior of the piece and gluing seems appropriate, we would recommend a two-part epoxy glue such as DP460 Epoxy Glue.
My piece was fired to a standard full fuse. Why did it crack? It had a 3mm white base with 3mm black and coloured glass on top, with dichroic highlights in places (2mm). (Image is of the back of the piece).
It looks like this crack was caused by thermal shock. There are a number of factors contributing to why the piece has cracked.
Dark colours will heat up quicker than light colours, dark colours absorb heat more readily than light colours like white which will reflect heat away and heat up more slowly.
Large pieces with large areas of contrast will exaggerate this effect, the size of your piece made it difficult for the temperature between the light areas and the dark areas to be evened out.
Iridised or Dichroic coatings will also reflect heat away causing a difference in rate at which different areas will heat up.
With all three of these factors combined in your piece it was vulnerable to thermal shock. To prevent this happening on future pieces and if you re-fire this piece, I recommend slowing down your heating and cooling rates, here is a more conservative firing schedule:
Is glass frost-proof?
All glass will take very low as well as very high temperatures. However, as soon as glass is made into something certain things will influence how frost proof they are, especially when there are rapid changes in temperature. Things influencing the strength of glass objects are:
- Design, variations in thickness (like a wine glass) reduces an objects ability to cope with rapid heat change.
- Poor annealing will leave permanent stress in the glass resulting in weakness which will cause the glass to crack.
If a design is even thicknesses and well annealed then it should be frost proof. To test to failure we put things in a plastic bag, freeze them overnight and then run them in the dishwasher. If they tolerate this they should survive outdoors without a problem.
Why did my piece crack when slumping it in an s-curve mould using the kiln's factory setting slump cycle?
The factory cycle of your plug-in kiln may be a bit harsh if the piece was thick. Also, the piece may have gripped the mould. If the edges are sharp then the glass cracked in cooling and this would indicate either cooling too fast or gripping the mould. If the edges of the cracks are soft, then the glass had stress in it before it was fired, it was heated too fast or it was too close to the elements. Take a look at our Successful Slumping in a Plug In Kiln tip sheet for more information, and always use the firing schedule appropriate to the specific mould, which if you bought it from us, can be downloaded from the product page for the mould.