Tools & Supplies
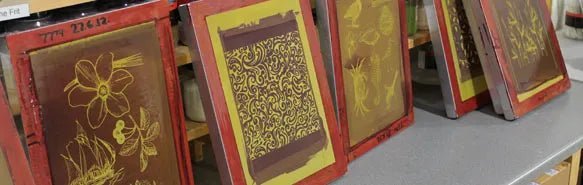
Tools & Supplies
Get the most out of your glass studio tools and equipment.
How do I drill a hole in glass?
Take a look at this video which demonstrates a hole being drilled in glass ready for a jewellery grommet to be fitted. This was done using a Dremel Multitool and diamond wire drill bit. Always immerse the drill bit in shallow tub of water when drilling to avoid burning off the diamonds. Risk of electrocution: Always use a cordless drill or flexible shaft when using near water.
What is the difference between each of the shelf primers you stock?
Shelf primer (or kiln wash) is used to prevent your glass from sticking to the kiln shelf or mould during firing. We sell an number of different types and each have their particular uses:
Bullseye Shelf Primer: Our most popular kiln wash, this is a good general purpose primer. It has a helpful pink tint so you can see exactly where you have applied it (the tint burns out on firing). It also dries quickly between layers and is easy to apply evenly with a soft haik brush. Another benefit is that if you fire under 706C, then you will not need to re-apply the primer for another firing. A new coating should be applied after a full fuse (766C or higher).
Hi-Fire Shelf Primer: An excellent shelf primer, this primer is specifically designed to perform well at high temperatures for techniques such as raking. It is also good for bead release and seems to work well at lower firing temperatures as well, making it a good all-round primer. It also has a pink tint to help show where it has been applied, and goes on nicely in even layers. It cleans from the shelf and glass easily after use.
Primo Primer: We recommend this primer for use with casting moulds, such as the Colour de Verre dragonfly mould or nano bead mould. Although slightly more difficult to mix and apply (Tip: leave it for an hour after adding the water before mixing again and applying), it is truly excellent at releasing work from these complex moulds, leaving great detail and a smooth finish. It also needs minimal clean up afterwards.
Boron Nitride Spray: It is expensive, but a little goes a long way and it is ideal for stainless steel moulds such as the floral former because, unlike other primers, you do not have to heat the mould for the primer to adhere. It also gives a fantastically smooth finish to your glass, minimising cold work. Not recommended for firing temperatures above product.
Bullseye Thinfire Paper: This product removes the need to prepare and apply a primer. A more expensive option than primers because the paper only lasts for one firing, but preparation times are almost zero. Just put the paper on the kiln shelf and place your work on top. Bullseye Thinfire leaves a very smooth finish too. We use this extensively in our studio.
For more information, see the product pages or watch our YouTube video: Help Me Choose: Shelf Primers.
My Thinfire paper is burning during firing? Why?
Thinfire paper is a ceramic material held together with organic binders, these binders will burn between 400-600°c it is normal to notice a burning smell and even a small amount of smoke in this temperature range. After the 600°c point all of the organic material will have burnt away and the paper will have turned into a white powdery material. The appearance of the Thinfire whilst it is burning is brown and smokey, this can be alarming but it is completely normal and nothing to worry about. Take a look at this video by Bullseye Glass to see what happens to Thinfire paper during the firing cycle: https://youtu.be/wqiYYF4SSfM
How can I learn to cut glass?
If you've never cut glass before, it's a good idea to take a class to teach you the basics of cutting glass, as well as the best tools and techniques to use. We also have a tip sheet on Improving Your Glass Cutting which contains some useful tips.
What is the Rule of Halves?
The Rule of Halves refers to cutting glass. A cut is much more likely to run smoothly if there are equal amounts of glass on each side of the score, hence the Rule of 'Halves'.
How do I coldwork a piece that I've cast?
The methods used to coldwork a kilncast piece can vary depending on exactly what needs doing to the piece. If a reservoir needs removing, this can be done using a tile saw with a diamond blade, by using rotary tools, or by hand lapping with loose grit. Diamond hand tools can be used to remove small imperfections on the surface of your casting, such as flashing - areas where glass has flowed into small cracks in the mould.
Please note: A casting should be at room temperature for 24 hours before any cold work is carried out. This is because even if a piece feels cold on the outside, it could be considerably warmer in the centre, so can still be subject to thermal shock.
Can I cast glass in a slumping mould?
Yes. Just remember to reapply primer after each firing.
Can I cast glass and clay together?
Glass and ceramic clay are not compatible. It may be possible to formulate a clay that is compatible with Bullseye glass, but as of yet this has not been achieved. Some ceramicists will incorporate glass experimentally in their pieces to create interesting effects, or for example by firing a clay pot with no base to glaze temperatures, then re-firing with glass frit in the bottom to produce a glass based pot.
Can I firepolish my casting?
Firepolishing happens at slumping temperatures, so flat pieces can be firepolished, but more upright pieces would be affected by the heat so are not suitable to be firepolished.
Can I make a casting mould that I can use again?
This is possible, as long as you make the correct investment mix. Castalot is an example of a great mix for creating reusable moulds.
I would like to glue glass to glass. What glue do you recommend that dries clear?
There are several options for glueing glass to glass, the simplest is silicone with aquarium silicone being the clearest. Single part silicone is good for glueing large areas together. Alternatively, professional laminating glues are available from Bohle and you can either use 2 part silicone glue or ultra violet curing glue, both are very strong and very expensive.
What product would you recommend to create moulds in which to cast glass? I would like to use it several times.
The best product for multiple glass casting is Castalot Casting Plaster.
What can I use fibre paper and fibre rope for?
Fibre paper and fibre rope are very versatile, and different thicknesses lend themselves to different tasks:
1mm fibre paper is useful for lining a box casting or for lining the base of your kiln. Some people use this fibre as a separator paper in place of kiln wash, however does not give as smooth a finish as Thinfire paper. Opal glasses tend to stick to fibre papers more than clear and transparent coloured glasses, for this reason we do not recommend fibre paper is used as a shelf separator unless it is used on combination with another separator such as Thinfire paper.
3mm Fibre Paper is great as a separator in box casting, lining the box or protecting dams. Just cut some strips and arrange them inside the box. You can also use 3mm fibre paper to add texture to glass in a simple process known as kiln carving. It can also be used to insulate against thermal shock and improve annealing, or you can cut and construct with it for bas relief design.
6mm Fibre Paper is also very versatile. As well as kiln carving, you can cut and construct with it for bas relief design or use it to form low profile dams when making pieces using frit. Use with fibre hardener to create rigid moulds that can withstand more than one firing.
We don’t recommend firing onto any of these fibres above 804C (for kiln carving) unless you are planning to do some coldworking.
Fibre rope can be used to create lateral holes in pendants. try using two strands of the rope to achieve a hole large enough for a necklace chain. Fibre rope can also be used in kiln carving to create shapes in glass.
To get started with kiln carving, try our Kilncarving Kit.
The fibre we sell is Biosoluble Fibre Paper. This is not the same as Ceramic Fibre (which we have never sold). The fibre paper we sell is made from an Alkaline-earth Silicate Wool, unlike Ceramic Fibre, AES Wool is bio-soluble and if inhaled does not accumulate in the lungs. This is an excellent alternative to ceramic fibre but it can be itchy so we recommend using a FFP3 Dust Mask when using this product, and cleaning up using a vacuum with a HEPA filter.
Which cutter is best, pistol grip or pencil grip?
It is simply a matter of personal taste. Some prefer the pencil grip while others like the pistol grip. We use both types regularly here at Warm Glass. For more information, take a look at our YouTube video: Help Me Choose... Glass Cutters.
I have been using fibre paper as a mould. I cut shapes then use my 'waste' glass (the very small pieces) in it. This works well but obviously I can only get one firing per piece of paper. I have noticed the fibre hardener on your site. If I was to soak the fibre paper in this product, would I get more than one firing with each 'mould'?
Yes the fibre hardener will make the fibre hard enough to use for repeated firings. However, you will need to use Primo primer or Bullseye shelf primer on the form to allow the glass to cleanly release. You can also use iridised glass against the mould for a clean release.
When I use the Candle Bridge mould, the glass pulls in at the edges on slumping. How do I prevent this?
To prevent the glass pulling in at the edges when it slumps into the top of the mould, make sure your glass is slightly wider (no more than 5mm) than the edge of the mould. This will stop the glass pulling in at the sides.
My breakers have become stiff and difficult to use. How do I prevent this?
If your breakers, or any similar tools, become stiff or begin to stick, make sure the mechanism is clear of debris and apply a small spray of WD40 lubricant. After a few minutes the tool should operate smoothly again. This should be done regularly as part of general maintenance of your tools.